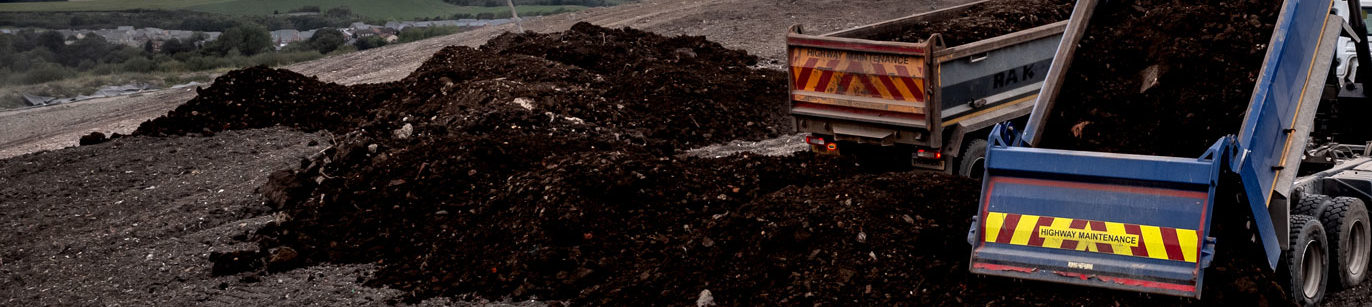
NewsOctober 6, 2023
SOPHISTICATED APPLICATIONS REQUIRE ACCURATE HYDRAULIC OIL CLEANING
One of the latest social media trends focusing on hydraulics is related to precision movements.
Skill challenges with cranes, creatively arranging timber in forestry, fast and harmonious gravel spreading with tippers are just a few examples.
Fun and entertaining videos, related to skill challenges, to be enjoyed in your free time.
What do they have in common?
The skill of the operators, of course, and the fluidity of the movements.
We are talking about entertaining moments, but it is clear that, in addition to the fundamental skill of the operators, the fluidity and precision of the hydraulic applications play a crucial role, with continuous and sometimes imperceptible movements that are fundamental to the success and efficiency of the daily work.
Fluidity, on the other hand, is linked to a clean fluid.
Pollution from dust, contaminants and metal debris from welding has always been a concern, but with the latest, even more sophisticated systems, it has become paramount.
What can be done to preserve the system and the investment?
This is our field, and we can say that when choosing between making or buying from a partner, among other things it is good to consider the cost of damages that could be generated on the system.
Indeed, manual welding brings with it the risk of weld debris when the metal is drilled through in the welding process or in so-called ‘rework’.
It must be considered that the sealing of cylinders and any other application components is vital both for the life of the system and to reduce the risk of hydraulic fluid leaking into the environment.
If metal debris or dust contaminates these components, sealing is no longer guaranteed.
Tens if not hundreds of thousands of euros or dollars are thus wasted and the costs to restore the application are considerable.
The industrialised tank, as we have said, is the first step, but the second is definitely the return filter.
It is sometimes considered an optional extra, often even a waste of time since the cartridge needs to be replaced twice a year or more (depending on the conditions of the working environment).
Someone even does not consider replacing the breather cartridge in the cap, which is also important, since a clogged cap does not compensate the air in the tank during suction and return phases, does not properly filter out air pollutants and, above all, carries the risk of tank implosion.
To recap: proper filtering and air exchange are fundamental.
We must consider, by way of example, that even tipper cylinders, although considered by many to be the most common and most durable type of application, owe their life to the quality of the oil.
How can the system be preserved from pollutants that are dangerous to the system?
The opportunities for filtration are “endless”, from immersed and semi-immersed filters to in-line and spin-on filters.
As a #tankspecialist company, we suggest the use of immersed or semi-immersed filters.
The reason for this is the convenience of the system, with the filter mounted directly on the tank, and that the cartridge is the only component to be replaced and disposed of.
Other solutions, such as spin-on, require more hoses to connect the filter to the tank and the tank to the system, in addition to the fact that the filter is completely disposed once it comes to the end of its life.
In case, moreover, space is limited, EasyFilter filters are available (360° rotation of the head and only 41 mm height) as well as the T20 hydraulic tank, with the body surface inclined at 20° to allow easy maintenance of the filter and cap.
Finally, do not forget the opportunity to fix the tipping valve on the tank with the EasyKit immersed filter with valve plate available in different holes layout for your specific distributor.
At Padoan you can count on a specialised and dedicated team, also providing support to OEMs, manufacturers and outfitters to find the most effective and efficient solution.
We are ready to work by your side to achieve your goals.
Download our
company brochure
Discover our catalogue, with all the detailed information about our products.
Download PDF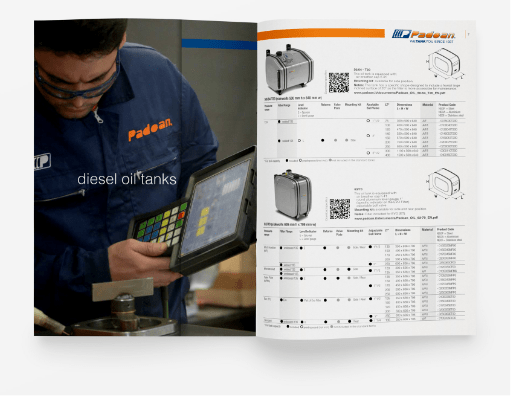